How to implement a digital system for monitoring assets, chemical parameters and infrastructure?
Jure Špeh, Co-founder and CTO
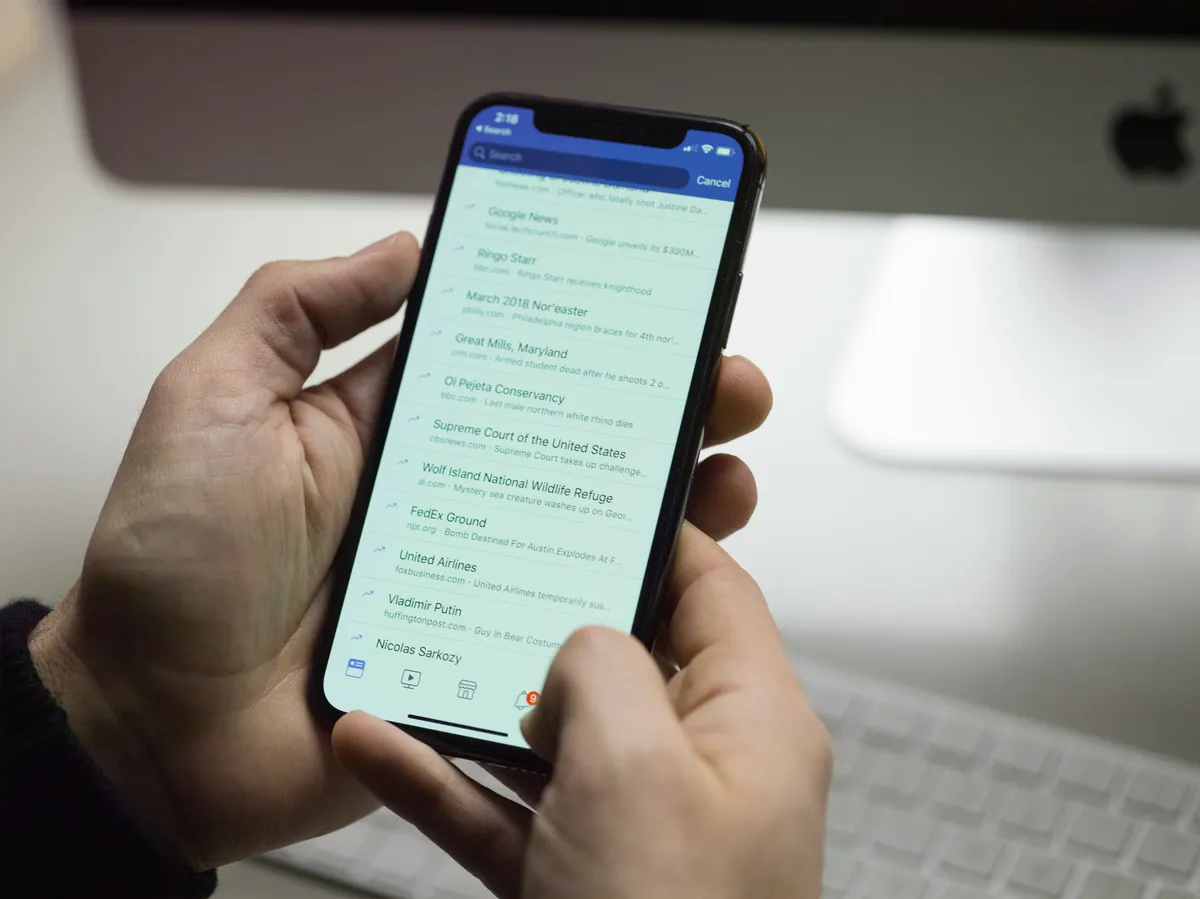
What are the phases of transition from paper records to digital solutions, and what are the challenges in this process.
Stages of implementing a digital system for monitoring assets and infrastructure
Utility, water supply and other companies that handle field infrastructure maintenance are at various stages of digitalizing field asset monitoring.
What are the phases of adopting digital solutions for field workers?
- Visits are carried out on an ad-hoc basis and by arrangement: This can pose a high risk to the safety and health of end users.
- Use of pencil and paper forms: Certainly a better solution, but in practice not used regularly. Forms are often filled out incorrectly or poorly, frequently in bad condition, or field workers simply do not return them to responsible persons. Oversight of field conditions is therefore limited, as is data analysis. Data must then be manually re-entered into digital form.
- Excel or Google Docs: A good step toward digitization, but it has two major drawbacks that limit its real-world use: the user experience on mobile phones is poor (complex to use and prone to errors), and it is unusable in remote locations without connectivity.
- Use of existing organizational information systems (ERP): Almost every organization uses one or more software solutions for managing procurement, accounting, GIS, inventory, and work processes. Most of these systems are older, so the user experience is suboptimal. They require lengthy onboarding, after which users are largely left to fend for themselves or rely on technical support. Another common issue is the high cost of individual modules.
- Use of dedicated software: Software designed for digitizing asset monitoring addresses all the drawbacks listed above and offers the most user-friendly solution. This type of software (such as TagPlan) is entirely tailored to planning field tasks and operating under any conditions. Key criteria for these solutions are ease of use, reliable performance in all environments, and regular updates. The vendor must be responsive and quickly resolve any operational issues. Despite these advantages, certain questions still arise when introducing such solutions into organizations—these are collected in the next section.
Status in practice
Some very small organizations may still be at stage one. Larger companies and institutions typically reach stage four. At this point, further adoption of new technologies and systems sometimes stalls due to resistance around using multiple software tools simultaneously.
This concern is understandable: each additional tool requires employees to learn a new application. However, this step becomes trivial if the application is intuitive and reliable, eliminating the need for lengthy training. This is exactly what we focused on when developing the TagPlan application for digital work orders and asset monitoring.
A single solution that covers every business process—from payroll and accounting to inventory management and field measurements—does not exist. Some platforms offer many of these features, but they cannot compete with specialized solutions when it comes to usability, user experience, and regular updates.
Why it makes sense to include TagPlan in your workflow
Instead of starting with technology, we conducted over 20 interviews with managers and field operators. This gave us insight into the real needs of decision-makers and the challenges field workers face. Using this knowledge, we developed a solution that makes adopting the final, fifth stage much easier, because the tool includes only the functionalities that field team leaders and operators need most.
If you are considering digitizing asset monitoring in the field, you can read the article listing the four most common concerns in this process.