How to Improve Monitoring Systems for Supervising Facilities and Utility Infrastructure
Jure Špeh, Co-founder and CTO
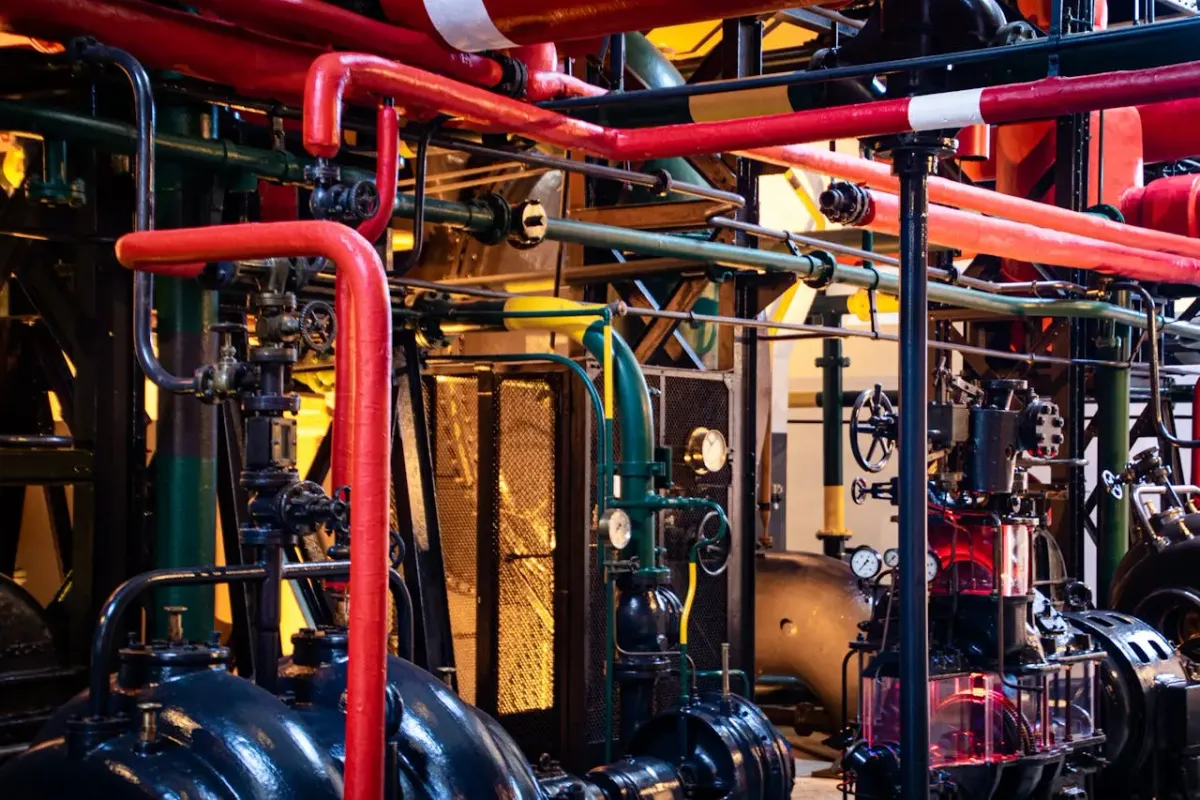
Why on-site inspections still matter—boost infrastructure oversight beyond SCADA with smarter field monitoring.
The Challenge of Infrastructure Oversight
Utility companies, municipalities, internal service departments, and public infrastructure operators must ensure the smooth daily operation and public appearance of the facilities they are responsible for. These can include both real estate and high-value movable assets.
Examples include:
- water catchments,
- pumping stations,
- reservoirs,
- wastewater treatment plants,
- public lighting,
- boiler rooms, furnaces,
- manholes,
- HVAC systems,
- green areas,
- elevators,
- bridges and other infrastructure.
Movable assets typically include work machinery that must be regularly maintained (e.g., excavators, trucks, tractors, specialized trailers, and other large machines).
There’s a widespread belief that additional infrastructure monitoring is unnecessary because such systems are already part of connected solutions like SCADA systems.
SCADA Systems and Infrastructure Monitoring
Many utility and public service companies have long been using systems for automated remote parameter monitoring (SCADA systems). Nevertheless, maintenance teams still carry out manual, in-person inspections of infrastructure. Some facilities are in remote locations without internet or mobile connectivity, making data transfer to a central system impossible—or the investment in a SCADA system simply isn’t justified.
Additionally, SCADA systems typically only monitor physical quantities, while other critical factors are often overlooked. That’s why regular on-site visits remain important.
The Role of Regular On-Site Inspections
For remote and critical sites, it’s essential that a technician or operator regularly visits the location to inspect key buildings, machines, and systems.
Common tasks at each site include:
- Visual inspection (e.g., cleanliness, pipe leaks, animal intrusion, mold, equipment damage)
- Checking and verifying system measurements (e.g., flow meters, free chlorine, turbidity, pH, pressure, temperature, aluminum levels, etc.)
- Performing calibrations (e.g., chlorine analyzers)
- Manual meter readings (double-checking the accuracy of automated readings)
- Taking samples for lab analysis
- Monitoring tank levels (e.g., fuel for generators, chemicals for water treatment)
- Recording completed tasks and observations during the visit (e.g., equipment repairs, part replacements)
- Reporting deviations from normal conditions (as a basis for follow-up work)
Every significant site should be visited daily, weekly, or at least monthly—depending on internal regulations, risk assessments, and the judgment of responsible personnel.
Organizations that have transitioned from the old method of infrastructure monitoring (based on gut feeling, without recorded data) to a structured system report improvements in site conditions, better water quality, greater oversight of equipment and frequent failures, and less stressful inspections by authorities.
A major benefit of digitizing field visits is the simplified onboarding of new employees or substitutions during vacations or sick leave. New staff can review past data, interventions, and site photos to quickly understand each facility and become productive faster. The same applies to temporary replacements.
Implementing a Systematic Field Monitoring Process Is a Key Step in Improving Organizational Performance